Infrasound Microphone - USB - IEPE - WS2F Industrial Standard
Low Frequency Measurement Microphone Class 1 - WS2F - DIN IEC 61094-4
iSV1611-Infra
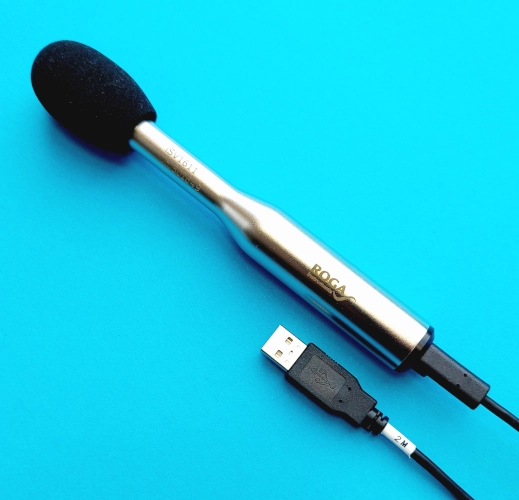
-
Price: 1625 €
68 € Shipping Price
- Frequency range 1 Hz to 20 kHz
- Free Field
- Measuring range 15 dB(A) to 135 dB
MP30-Infra
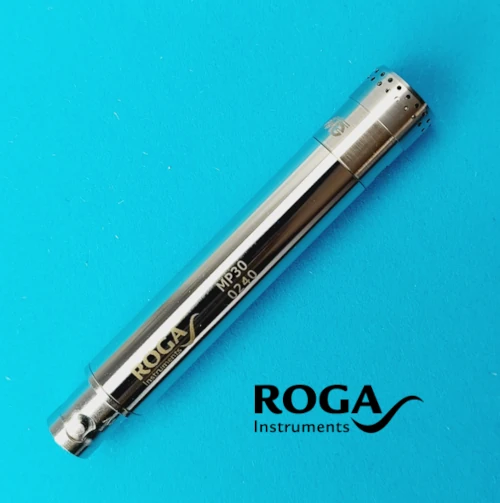
- Price: 1446 €
- MP30-Infra Datasheet
- Sensitivity 50 mv/Pa
- IEPE constant current supply 2-20 mA
- Directional characteristic: omnidirectional
- Frequency response: 0.5 Hz – 20 kHz (± 2 dB)
- 0.5 Hz – 3.5 Hz: ± 2 dB
- 3.5 Hz – 4 kHz: ± 0.5 dB
- 4 kHz – 20 kHz: ± 2 dB
- Acoustic noise floor 15 dB A-weighted
- Measuring range 15 dB(A) to SPL peak (5% dist.) 135 dB
MK 222 E Microphone Capsule | IEC 61094-4 Type WS2F |
---|---|
Diameter | 1/2″ |
Frequency Range | 0.5 Hz ~ 20 kHz (±2 dB) |
Responce Type | Free field |
Electrode Forming Voltage | 0 V |
Sensitivity (dB re 20 μPa) | 50mV/Pa (±1.5dB) |
Capacitance at 250 Hz | 18 pF |
Maximum Sound Pressure Level | 135 dB |
Intrinsinc Noise Level | 15 dB (A) |
Operating Temperature Range | 10℃~+ 50℃ |
Operating Humidity Range | up to 70 °C, 90 % |
Temperature Characteristics |
< 0.015 dB/°C |
Humidity Characteristics | 0.001 %(RH) |
Aging Drift | 0.2 dB/Year |
Storage Temperature Range | -20 °C ~ +60 °C |
Storage Humidity Range | 25 % ~ 90 %(RH) |
Venting |
rear vented |
Outer Dimensions | Ф 13.2 mm x 10.9 mm |
Weight | 8.3 gram |
iSV1611 | USB Microphone Preamplifier |
---|---|
Signal Amplitude ref. 50mV @ 1kHz Frequency Response Frequency Sampling 192 kHz |
1 Hz~20Hz, Error <3.0dB 20 Hz~20kHz, Error<0.3dB 20 kHz~80kHz, Error<3dB |
Electrical signal noise background | Ch.1 (<13dBA, <26dBZ) Ch.2 (<50dBA, <63dBZ) |
THD
Input 1kHz, 50mV, A weighting | <0.1%
|
Overload Indicator 1kHz (THD<3%) | Ch.1 (>101.9dB) Ch.2 (>140dB) |
Amplitude accuracy Input 31.6mV, 1kHz, 90.0dB | Error <0.2dB
|
Dimensions 1/2″ Outer diameter of protector cover | Ф 20 × 165 mm φ 13.2mm |
Weight | <96 g (cable not included) |
Operating Temperature | -20°C ~ + 60°C |
Humidity | 25 %~ 90 %(RH) |
Atmospheric Pressure | 65 kPa~108 kPa |
Connector Type | USB2.0, |
Microphone Thread | 11.7 mm-60 UNS |
A ROGA microphone on a stratospheric balloon
The BEXUS-ARESONUS experiment at Nordhausen University of Applied Sciences
Prof. Dr.-Ing. Matthias Viehmann, Nordhausen University of Applied Sciences, July 2025
Image 1: Launch of BX 35 at the launch crane
Figure 2 shows the system structure and components. The ROGA iSV1611-Infra with MTG MK 222 E SN-26112 was used. This was housed in a microphone tube that protruded downwards next to the main module. The tube also contained a temperature sensor and a piezoelectric transducer. The transducer was activated cyclically and served as the acoustic system heartbeat.
Image 2: System structure and main module with microphone tube (right)
With the system’s return, the team began the system status and data analysis phase, see Figure 3. Signal acquisition and data recording took place throughout the entire flight. Several acoustic events could already be attributed to the microphone signals, for example: the heartbeat transducer, the activity of the combustion engine from the launch crane, the flybys of two aircraft, the airflow noise as the gondola descended on the parachute, and the landing impact.
Image 3: BEXUS-ARESONUS team behind the flown system (from left)
Ria Bele Pohley, Prof. Viehmann, Sabine Köhler, Johann Stiebritz, Niclas Bierwisch, Sven Malag, Prof. Neitzke
All team members would like to thank ROGA for their friendly and reliable support in the form of providing microphone technology and expert advice!